История открытия сплавов
Сплавы на основе системы Al-Zn-Mg-Cu обладают наивысшей прочностью до 800МПа в долевом направлении для прессованных полуфабрикатов среди алюминиевых сплавов. Они имеют особенно высокий предел текучести, который на 40—50 % выше, чем у сплавов типа Д16 в естественно состаренном состоянии Т. Развитие высокопрочных сплавов началось с открытия в 1923—1926 гг. немецкими учеными Зандером и Мейснером чрезвычайно высокого эффекта закалки и старения в трехкомпонентных сплавах Al-Zn-Mg.
В начале 40-х годов был разработан сплав В95 (табл. IV. 1). Он нашел широкое промышленное применение как высокопрочный сплав и до настоящего времени наряду со сплавом Д16Т является основным конструкционным материалом авиационной техники. В 1956 г. И. Н. Фридляндер и Е. И. Кутайцева создали более прочный сплав В96Ц, в который впервые в мировой практике был введен цирконий вместо марганца и хрома. Это позволило повысить пластичность и улучшить прокаливаемость высокопрочных сплавов. Позднее были разработаны еще два сплава с цирконием — самый прочный сплав В96Ц-1 (в основном для прессованных полуфабрикатов) несколько менее легированный, ковочный сплав В96Ц-3 С высокой технологической пластичностью.
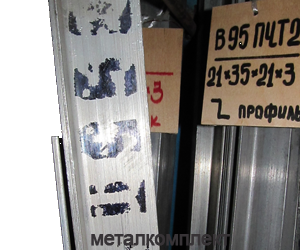
В 1957 г. для изготовления массивных поковок и штамповок создан оригинальный отечественный сплав В93, который легирован небольшим количеством железа взамен традиционных элементов — антирекристаллизаторов марганца, хрома, циркония. Это обеспечило повышенную прокаливае-мость и однородность прочностных свойств во всех направлениях при хорошей технологичности литья, ковки, штамповки.
Специально для заклепок разработан сплав В94, обладающий хорошей расклепываемостью в искусственно состаренном состоянии и сопротивлением срезу в расклепанном состоянии. По сравнению со среднепрочными сплавами высокопрочные сплавы менее пластичны и более чувствительны к надрезам, перекосам, что необходимо учитывать при обработке деталей и сборке конструкций из них. При применении сплавов еледует тщательно подходить к конструированию деталей: выбирать формы с минимальными концентраторами напряжений, с большой плавностью переходов при изменении сечения, уменьшать экцентриситеты.
Высокопрочные сплавы не теплопрочны и при длительной эксплуатации их можно использовать до температур не выше 100—120°С.
На первом этапе применения основных высокопрочных сплавов В95 и В93 главное требование, предъявляемое к ним, состояло в обеспечении максимальной статической прочности С учетом этого был установлен химический состав сплавов с довольно широкими допусками на содержание примесей железа и кремния и режим термообработки Т1, отвечающий фазовой стадии старения . При этом полуфабрикаты из таких сплавов обычной чистоты по примесям в состоянии Т1 имели ряд недостатков, к числу которых следует отнести склонность к коррозионному растрескиванию и расслаивающей коррозии, большую чувстви-тельность ко всякого рода концентраторам напряжений, пониженную пластичность и статическую выносливость.
В 60-е годы обострилась проблема надежности, долговечности, экономичности современной техники, что существенно изменило подход к оценке работоспособности высокопрочных сплавов. Они юлжны обладать оптимальным комплексом свойств: высокая прочность должна сочетаться с высоким сопротивлением коррозии и усталости и с достаточно высокими значениями характеристик пластичности и трещиностойкоси, введенных в расчеты при проектировании самолетных конструкций по новому принципу безопасной повреждаемости.
Поэтому для дальнейшего надежного и эффективного применения высокопрочных сплавов были разработаны новые модификации с ограниченным содержанием примесей железа и кремния (а для сплава В95 с одновременным снижением концентрации цинка) — сплавы В95пч, В95оч и В93пч повышенной и особой чистоты. Это позволило существенно повысить пластичность и трещиностойкость при сохранении статической прочности и некотором увеличении сопротивления малоцикловой усталости.
Задача кардинального повышения стойкости к коррозми под напряжением и расслаивающей коррозии при дополнительном увеличении сопротивления разрушению сплавов была решена в результате разработки новых двухступенчатых режимов коагуляционного старения Т2 и Т3. Эти режимы называют также смягчающими, так как они приводят к небольшому разупрочнению (на 10—15%) по сравнению с режимом Т1. По коррозионной стойкости сплавы В95пч, В95оч и В93пч в состояниях Т2 и Т3 значительно превосходят сплавы типа дуралюмин.
Сплав | Основные компоненты | Примеси (не более) | ||||||||||
Zn | Mg | Сu | Мn | Сг | Другие | Fe | Si | Мn | Ti | Прочие | ||
Каждая | Сумма | |||||||||||
В93 | 6,3-7,3 | 1,6-2,2 | 0,8-1,2 | - | - | Fe 0,2-0,45 | - | 0,2 | 0,1 | 0,1 | 0,05 | 0,1 |
В94 | 5,9-6,8 | 1,2-1,6 | 1,8-2,4 | - | - | Ti 0,02-0,08 | 0,2 | 0,2 | 0,1 | 0,05 | 0,05 | 0,1 |
В95 | 5,0-7,0 | 1,8-2,8 | 1,4-2,0 | 0,2-0,6 | 0,1-0,25 | - | 0,5 | 0,5 | - | 0,05 | 0.05 | 0,1 |
В96 | 7,6-8,6 | 2,5-3,2 | 2,2-2,8 | 0,2-0,5 | 0,1-0,25 | - | 0,5 | 0,3 | - | 0,05 | 0,05 | 0,1 |
В96ц | 8,0-9,0 | 2,3-3,0 | 2,0-2,6 | - | - | Zr 0,1-0,2 | 0,4 | 0,3 | 0,1 | 0,03 | 0,05 | 0,1 |
1915 | 4,0-5,0 | 1,0-1,8 | 0,1 | 0,2-0,7 | 0,06-0,2 | Zr 0,08-0,2 | 0,4 | 0,35 | - | 0,01-0,06 | 0,05 | 0,1 |
1925 | 3,4-4,0 | 1,3-1,8 | 0,8 | 0,2-0,7 | 0,2 | Zr 0,1-0,2 | 0,7 | 0,7 | - | 0,1 | 0,05 | 0,1 |
Легирующие элементы
Цинк, магний и медь образуют с алюминием и между собой твердые растворы и различные металлические соединения — MgZn2, S(Al2CuMg), T(Mg4Zn3Al3), играющие большую роль в упрочнении сплава при его термической обработке. В сплавах данного типа особенно важной является фаза T, находящаяся в равновесии с твердым раствором а (см. диаграмму Al—Mg—Zn на рис).
Марганец и хром усиливают эффект старения и повышают коррозионную стойкость сплава; марганец, кроме того, способствует получению мелкозернистой структуры, затрудняет выделение металлических фаз по границам зерен твердого раствора, а также несколько повышает прочность сплава; при этом особенно повышается прочность прессованных изделий, что характеризует так называемый «пресс-эффект». Пресс-зффект связывают с выделением мелкодисперсных частиц марганцовистой фазы или образованием блоков внутри зерен твердого раствора.
Термообработка
Максимальные значения прочности полуфабрикатов из сплавов на основе системы Al—Zn—Mg—Си достигаются при температурах закалки 460—475°С с последующим искусственным старением. Режимы старения: сплава В93 — ступенчатый (120°С — 3 ч + 165°С — 4 ч); сплава В94 — ступенчатый (100° С — 3 ч + 165°С — 3 ч); сплава B95— плакированные листы — 120°С 24 ч; сплавов В95 — неплакированные полуфабрикаты, В96, В96ц — 135-145°С в течение 16 ч или ступенчатый (120°С — 3 ч + 160°С — 3 ч).
Прочность и пластичность
Сплавы на основе системы Al—Zn—Mg—Си обладают высокой прочностью и пониженной пластичностью. Чувствительны к надрезам. в закаленном и искусственно состаренном состоянии, отличаются удовлетворительной общей коррозионной стойкостью, однако склонны к коррозионному растрескиванию под напряжением (в особенности сплавы В96 и В96ц). Коррозионная стойкость естественно состаренных сплавов неудовлетворительная. Детали из этих сплавов следует анодировать и защищать лакокрасочными покрытиями.
Недостатками сплавов типа В95 являются пониженная пластичность, повышенная чувствительность к концентрации напряжений, большая анизотропия свойств в поперечном и продольном направлении волокон и склоннюсть к коррозии под напряжением. Однако при правильной обработке, рациональном применении в конструкции и надлежащей защите от коррозии эти недостатки могут быть успешно устранены.
Марка | Обозначение |
Состояние образцов | Толщина листа, мм | Механические свойства при растяжении | ||
Временное сопротивление σв, МПа (кгс/мм2) |
Предел текучести σ0,2, МПа (кгс/мм2) |
Относительное удлинение при l=11,3√F* δ % |
||||
Не менее | ||||||
*Для испытаний используются длинные образцы,где l-участок образца в мм, на котором определяют удлинение,а F-начальная площадь поперечного сечения в рабочей части образца в мм2 |
||||||
В95А | В95AM | Отожженные | От 0,5 до 10,5 | Не более 245 (25,0) | — | 10,0 |
В95АТ1 | Закаленные и искусственно состаренные | От 0,5 до 1,9 | 480(49,0) | 400(41,0) | 7,0 | |
Св. 1,9 до 6,0 | 490 (50,0) | 410(42,0) | 7,0 | |||
6,0 до 10,5 | 490 (50,0) | 410(42,0) | 6,0 | |||
В95А | Закаленные и искусственно состаренные | От 5.0 до 10,5 | 490 (50,0) | 410(42,0) | 6,0 | |
В95—2А, В95—2Б, В95— 1А, В95— 1, АКМБ, АКМА, АКМ |
В95-2АМ, В95-2БМ, В95-1АМ, АКМБМ, АКМАМ, АКММ |
Отожженные | От 1,0 до 10,5 | Не более 245 (25,0) |
— | 10,0 |
В95-2А, В95—2Б, В95-1А, В95— 1, АКМБ, АКМА, АКМ |
АКМАН | Нагартованные | От 0,8 до 4,0 | Не испытываются | ||
В95-2АТ, В95-1АТ, АКМАТ |
Закаленные и естественно состаренные | От 1,0 до 10,5 | 315(32,0) | — | 10,0 | |
В95-2А | Без термической обработки | От 5,0 до 10,5 | 315(32,0) | — | 10,0 | |
В95-1А, В95-1, АКМА |
Не испытываются | |||||
1915 | 1915М | Отожженные | От 1,0 до 4,5 | Не более 245 (25,0) |
— | 10,0 |
1915Т | Закаленные и естественно состаренные в течение 30—35 суток | От 1,0 до 10,5 | 315 (32,0) | 195(20,0) | 10,0 | |
1915Т | Закаленные и естественно состаренные в течение 2-4 суток | От 1,0 до 10,5 | 275(28,0) | 165(17,0) | 10,0 | |
1915 | Закаленные и естественно состаренные в течение 30-35 суток | От 5,0 до 10,5 | 315(32,0) | 195(20,0) | 10,0 | |
1915 | Закаленные естественно состаренные в течение 2-4 суток | От 5,0 до 10,5 | 265(27,0) | 165(17,0) | 10,0 | |
ВД1А, ВД1Б, ВД1 | ВД1АМ, ВД1М, ВД1БМ |
Отожженные | От 0,8 до 10,5 | Не более 245 (25,0) |
— | 10,0 |
ВД1АТ, BД1T, ВД1БТ |
Закаленные и естественно состаренные | От 0,8 до 10,5 | 335(34,0) | — | 12,0 |
Использование
Сплав В95 хорошо сваривается точечной сваркой; сплавы В96 и В96ц удовлетворительно свариваются аргонодуговой сваркой. Пластичность сварного шва пониженная.
Все сплавы на основе системы Al—Zn—Mg—Си хорошо обрабатываются резанием.
Сплавы В93, В95, В96, В96ц применяют для изготовления нагруженных силовых деталей и конструкций в различных отраслях техники. Сплав В94 применяют для изготовления заклепок и заклепочной проволоки.
При длительной эксплуатации рабочие температуры изделий из сплавов на основе системы Al—Zn—Mg—Сu не должны превышать 100°С
Полуфабрикат | Состояние материала | σв | σ0,2 | δ % |
кгс/мм2 | ||||
Не менее | ||||
*Свойства в поперечном направлении **Механические свойства особо прочных листов обеспечиваются путем ограничения содержания магния и цинка в сплаве и отбором листов серийно поставляемой продукции. |
||||
Листы плакированные толщиной, мм *: 0,5–10,0 |
Отожженные | 25 | - | 10 |
0,5–1 9 | Закаленные и искусственно состаренные | 49 | 41 | 7 |
2,0–6,0 | 50 | 42 | 7 | |
6,1–10,0 | 50 | 42 | 6 | |
1,2–6,0 | Закаленные и искусственно состаренные, особо прочные** | 63 | 46 | 6 |
6,1–10,0 | 53 | 46 | 5 | |
Профили с толщиной стенки, мм: ≤10 |
Закаленные и искусственно состаренные | 50 | 45 | 6 |
≥10 | 52 | 47 | 6 | |
Прутки прессованные диаметром, мм: ≤22 |
50 | 40 | 7 | |
23–100 | 54 | 43 | 6 | |
300 | 50 | 43 | 5 | |
Трубы прессованные с толщиной стенки, мм: 5–20 |
50 | 38 | 7 | |
≥20 | 52 | 41 | 5 |
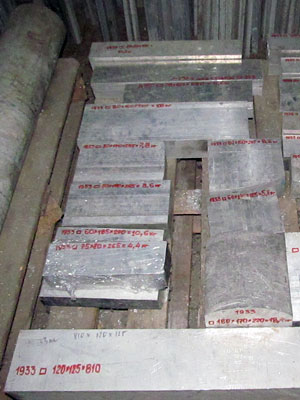